Table des matières
Introduction
Les émulsions de bitume sont utilisées dans le domaine routier pour la construction de nouvelles routes et pour l’entretien du patrimoine. Certains pays en pointe dans ce domaine, comme la France, emploient près de 30% du bitume sous cette forme. Le Chili ou encore l’Ireland vont même au-delà, tandis que d’autres ont du mal à monter dans le train de l’émulsion, en se limitant aux couches d’accrochage ou en poursuivant l’utilisation de liants fluidifiés.
Pourquoi formuler ses émulsions de bitume ?
La France produit chaque année environ 800 000 tonnes d’émulsions, soit près de 10% de la production mondiale, ce qui la place 4ème pays producteur au monde en 2022, derrière la Chine (1er avec plus de 2,4 millions de tonnes) les Etats-Unis (2nd avec 2,1 millions de tonnes) et le Brésil. L’analyse des données mondiales recueillies par l’IBEF (International Bitumen Emulsion Federation) permet de voir que d’autres pays misent sur le développement des techniques à l’émulsion pour développer leur réseau routier. C’est le cas par exemple du Mexique, de la Thaïlande, de Brésil, de l’Espagne, du Maroc, de l’Afrique du Sud, du Chili ou encore du Pérou.
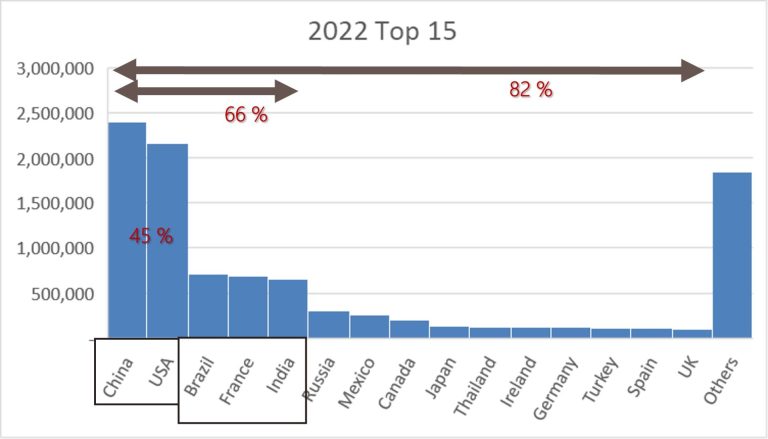
Principaux pays producteurs d’émulsions en 2022 (IBEF)
Dans tous ces pays où les émulsions se développent, parfois pour des raisons différentes, une constante reste vraie : l’importance de la maîtrise de la formulation. Car si les techniques d’enrobage à chaud traditionnelles nécessitent le répandage d’émulsions d’accrochage « simples » lors de la mise en place pour solidariser les différentes couches d’une chaussée entre elles, les techniques à l’émulsion, dites « à froid », nécessitent l’apprentissage des principes de base (physiques et chimiques) qui permettent de maîtriser la stabilité du bitume sous cette forme vectorisée transitoire. Seule l’acquisition de cette maîtrise rend possible le développement d’autres applications, comme les enduits superficiels d’usure, les matériaux bitumineux coulés à froid, les enrobés stockables à froid pour le bouchage d’urgence des nids de poule, ou encore les émulsions de recyclage permettant la réutilisation in situ de la ressource minérale déjà mobilisée. De la capacité de formulation d’une entreprise découle la performance de ses applications, par l’adaptation de ses produits aux conditions climatiques du chantier et aux matières premières disponibles localement.
Cette autonomie de formulation donne à l’industriel la capacité de s’adapter, d’améliorer et d’accroître son aptitude à répondre aux enjeux actuels mais aussi futurs, qu’ils soient d’ordre économique ou environnemental. Et nous sommes chanceux : les émulsions sont très efficaces dans ces deux domaines.
Acquérir l’autonomie
Au sein des entreprises de travaux routiers, le laboratoire de contrôle est parfois perçu comme une structure de coûts. Mais compte tenu de la sensibilité des techniques à l’émulsion à de multiples paramètres (qualité des matériaux minéraux, organiques, chimiques, moyens matériels et humains), le laboratoire est un acteur incontournable de la maîtrise. Ce qui peut sembler évident l’est parfois moins lors de la mise en service de nouvelles unités de production. Pourtant, une émulsion d’accrochage, aussi « simple » et « invisible » soit-elle une fois recouverte de l’enrobé, constitue une des clés de la durabilité d’un revêtement routier. Sa réussite doit mobiliser l’attention tout autant que la couche de surface. Le laboratoire est alors le centre névralgique du développement des compétences, avant transfert des formules établies en usine, où les erreurs, qui impliquent fatalement des quantités de matériaux importantes, sont ainsi évitées.
En effet, la production industrielle d’émulsion implique des unités de production dont le cœur est constitué d’un moulin colloïdal, comme l’homogénéiseur ATOMIX®, breveté en 1933 et fabriqué par VIALAB. Ces moulins permettent la dispersion du bitume sous forme de fines gouttelettes dans une phase aqueuse soigneusement formulée. Ces outils sont en général dimensionnés pour produire de 5 à 30 tonnes/heure. Leur démarrage implique a minima la fabrication de 3 à 5 tonnes d’émulsion. Avec de tels outils, adapter une formule ne peut se faire qu’à l’instinct, par de petites modifications quantitatives pour éviter les échecs coûteux. Le test de nouveaux composants, comme un bitume, un émulsifiant, un additif ou des variations de proportions, ne peut être envisagé sans risquer d’engendrer des pertes aussi volumineuses qu’onéreuses.
La solution se trouve donc au laboratoire, par l’utilisation d’outils dédiés. Les Pilotes de Laboratoire, avec lesquels des dizaines de conditions différentes peuvent être testées sans générer de pertes significatives en matériaux, sont de véritables mini-usines utilisables dans des étapes de pré-formulation et de contrôles de matériaux, jusqu’à la production des émulsions les plus complexes impliquant des bitumes durs, ou modifiés aux polymères, et dont le bilan thermique impose le travail sous pression.
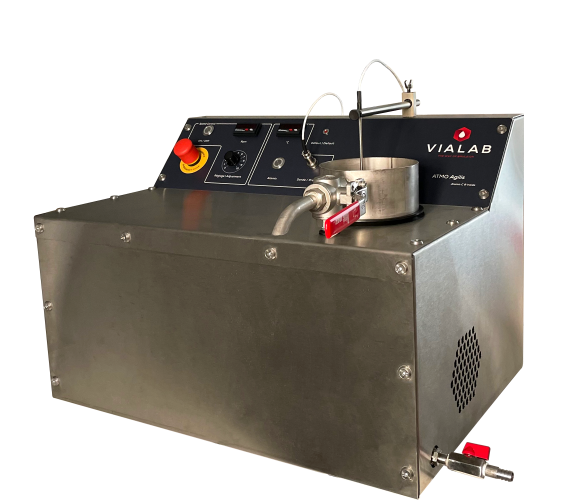
Pilote de laboratoire ATMO Agilis
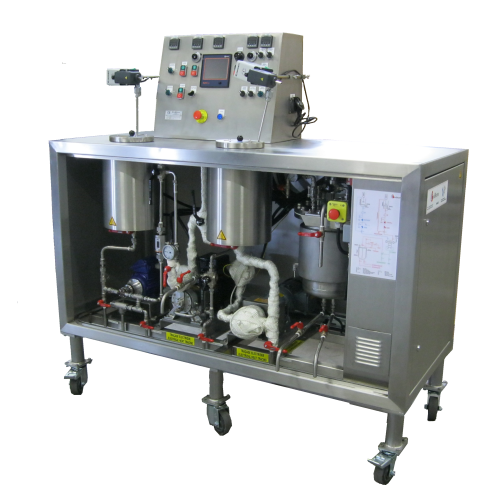
Pilotes de laboratoire PMB Polyvalens et ATMO Processus
Ainsi équipé, le laboratoire est capable de tester les performances de ces émulsions, a priori plutôt qu’a posteriori, en maîtrise plutôt qu’à ses dépens. En faisant varier la teneur en tensioactif, le formulateur ajuste précisément le comportement à la rupture de son émulsion en fonction des matériaux du chantier, tout en adaptant sa viscosité en fonction du support d’application, de la saison et des conditions météorologiques. Cette prise d’autonomie devient synonyme d’anticipation, et va de paire avec l’acquisition d’une expérience nouvelle, de compétences techniques, qui permettent la formation et la sensibilisation de tous les acteurs de l’entreprise, de la production jusqu’à l’application. En outre, le formulateur développe les compétences qui lui permettent d’optimiser ses interactions avec son partenaire fournisseur de tensioactifs et d’additifs, pour aller plus loin dans la maîtrise.
En d’autres termes, la compétence laboratoire en matière de formulation des émulsions permet à l’entreprise de sortir de l’empirisme, de gagner en expertise, de maîtriser ses coûts de production, de réduire le risque d’échec sur chantier. Le laboratoire est un investissement qui rapporte, est rapidement !
Se tourner vers l’avenir
Depuis plusieurs années, et de façon encore plus nette à partir de 2021, où la crise sanitaire a ajouté une pression supplémentaire au secteur de la construction routière, nous assistons au renforcement des attentes sociétales en termes d’environnement. La preuve a déjà été faite que les techniques à l’émulsion répondent aux attentes économiques autant qu’environnementales. Les quantités moindres de matériaux engagées, l’absence de séchage des granulats, la possibilité de recyclage en place des chaussées existantes par des liants spécifiquement formulés et l’utilisation de liants de substitution sont autant de solutions pour relever les défis qui nous font face. En Europe par exemple, des projets ont vu le jour, qui visaient à constituer une base de données des pratiques les plus vertueuses en matière d’environnement. Le projet collaboratif TRACC-Expert (France, Portugal, Espagne) puis TRACC-France (pour Techniques Routières Atténuant le Changement Climatique), a impliqué de nombreux acteurs publics et privés du secteur (CEREMA, Conseil Départemental, SPRIR, IDRRIM, IFFSTAR et beaucoup d’entreprises) dans un but commun. Ces projets ont abouti au développement d’un logiciel d’aide à la décision.
L’accès aux techniques à froid n’est pas aisé : la compétence est bien présente au sein des grands groupes, où le savoir se transmet de génération en génération, mais elle est plus difficile à acquérir dans les entreprises qui ne la détiennent pas, et les volumes de formations théoriques et techniques restent faibles, chez les techniciens comme chez les cadres. C’est la raison pour laquelle, en plus d’une gamme d’unités industrielles et d’équipements de laboratoire centrée sur les émulsions, VIALAB propose des formations complètes et concrètes, permettant aux entreprises d’acquérir la compétence et de consolider leur savoir-faire.
Rédigé par Vincent HESRY, CEO de VIALAB
Contenu associé :