Table of contents
Introduction
Bitumen emulsions are used in the road sector for the construction of new roads and for maintenance. Some countries at the forefront in this field, such as France, use more than 30% of bitumen in this form, while others are confined to their simple application as a tack coat, or even continue to use cutbacks binders.
Why should you formulate your bitumen emulsions ?
France produces around 800,000 tons of emulsions each year, or nearly 10% of world production, which places it 4th producer country in the world, behind China, the United States and Brazil. However, this tonnage compared to the size of the road network places France as a major player with 0.7 ton of emulsion per kilometer of road. Analysis of global data collected by the International Bitumen Emulsion Federation (IBEF) shows that other countries are betting on the development of emulsion techniques to develop their road networks. This is the case, for example, in Mexico, Thailand, Canada, Spain.
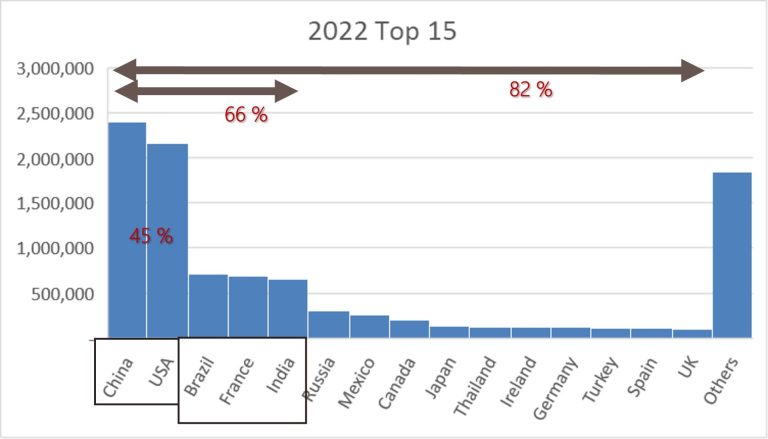
In all these countries where emulsions are developing, sometimes for different reasons, one constant appears: the acquisition of mastery of the formulation. Because if the traditional hot mix techniques require the spreading of “simple” bonding emulsions during application, to stick the different layers of a pavement together, emulsion techniques, so called “cold techniques”, require the learning of the basic principles (physical and chemical) which make it possible to control the stability of the bitumen in this transitory vectorized form. Only the acquisition of this expertise makes it possible to develop other applications, such as surface dressings, slurry- and micro-surfacing, cold-storable mixes for emergency pothole plugging, or even recycling emulsions allowing the in situ reuse of the mineral resource already mobilized. The formulation capacity of a company will improve the performance of its applications, by adapting its products to the climatic conditions of the site or to locally available raw materials.
This formulation autonomy will give manufacturers the ability to adapt, improve and increase their ability to respond to current and also future challenges, whether they are of an economic or environmental nature. Should we remember that cold techniques are very effective in these two areas?
Become independent
Within road industry, the control laboratory is sometimes seen as a cost structure. But given the sensitivity of emulsion-based technology to multiple parameters, such as the quality of mineral and organic materials, chemicals, equipment and human resources, the laboratory is becoming a key player in control. This evidence in the most advanced countries is sometimes not suspected when commissioning new production units in other countries. However, a tack coat emulsion, how “simple” and “invisible” it may be once covered with the asphalt it sticks, is one of the keys to the sustainability of a road surface. As much attention as for the asphalt must be paid. The laboratory becomes the center for skills development, before transferring formulas established in the factory, where errors, which inevitably involve large quantities of materials, are avoided.
Indeed, industrial emulsion production involves production groups whose core consists of a colloid mill, such as the Atomix® mill, patented in 1933 and manufactured by the Emulbitume Company. These mills allow the dispersion of bitumen in the form of fine droplets in an objectively formulated aqueous phase. These tools are generally sized to produce 5 to 30 tonnes / hour. Their start-up involves at least the production of 3 to 5 tonnes of emulsion. With such tools, adapting a formula can only be done on instinct, with small quantitative changes to avoid costly failures. The testing of new materials, such as bitumen, an emulsifier, an additive or variations in proportions, cannot be considered methodically because this would involve quantities as large as they are expensive
The solution is therefore found in the laboratory, through the use of dedicated tools. Laboratory Pilots, with which dozens of different conditions can be tested without generating significant material losses, are real mini-plants that can be used in pre-formulation or material control stages, up to the production of the most complex emulsions involving hard bitumen, or polymer modified bitumen, and whose heat balance requires work under pressure.
Laboratory pilots PMB Polyvalens and ATMO Processus
Thus equipped, the laboratory becomes capable of testing the performance of these emulsions, a priori rather than a posteriori, in control rather than at its expense. By varying the surfactant content, the formulator precisely adjusts the breaking behavior of his emulsion according to the materials used on the site. Or, it adapts its viscosity according to the application support, the season or the weather conditions. This empowerment becomes synonymous with anticipation, and goes hand in hand with the acquisition of new experience and technical skills, which will allow the training and awareness of all stakeholders in the company, from production to the application. In addition, the formulator will develop the skills that will allow him to optimize his interactions with his partner supplier of surfactants and additives, which was until then his sole source of control.
In other words, laboratory expertise in emulsion formulation enables the company to break out of empiricism, gain expertise, control production costs, and reduce the risk of failure on site. It’s an investment that pays off!
Look in the future
For several years, and even more clearly from 2021, where the health crisis added additional pressure to the road construction sector, we have been witnessing the strengthening of societal expectations in terms of environment. Proof has already been made that emulsion techniques meet both economic and environmental expectations. The smaller quantities of materials used, the absence of drying of the aggregates, the possibility of recycling existing pavements in place with specifically formulated binders or the use of substitute binders are all potential solutions to meet the challenges facing us. In Europe, for example, projects have emerged aimed at building up a database of the most virtuous environmental practices. The collaborative project TRACC-Expert (France, Portugal, Spain) then TRACC-France, involved many public and private actors in the sector (CEREMA, Departmental Council, IDRRIM, IFSTTAR and many companies) for a common purpose. These projects resulted in the development of decision support software.
Unfortunately, access to cold techniques is not easy. Skill is present in big companies or groups, where knowledge is passed on from generation to generation, but it is more difficult to acquire in companies that do not have it, the volumes of theoretical and practical training of future young technicians and managers on these technics remain weak, despite the high percentage of bituminous binders applied under emulsion form. This is the reason why, in addition to an offer in laboratory equipment focused on emulsions, Vialab offers theoretical and practical training, allowing companies to acquire skills or consolidate their know-how.
Vincent HESRY, CEO of VIALAB
Related content :
Everything about the production of PMB
The role of water in bitumen emulsions